Understanding Injection Mold Manufacturing: The Backbone of Metal Fabrication
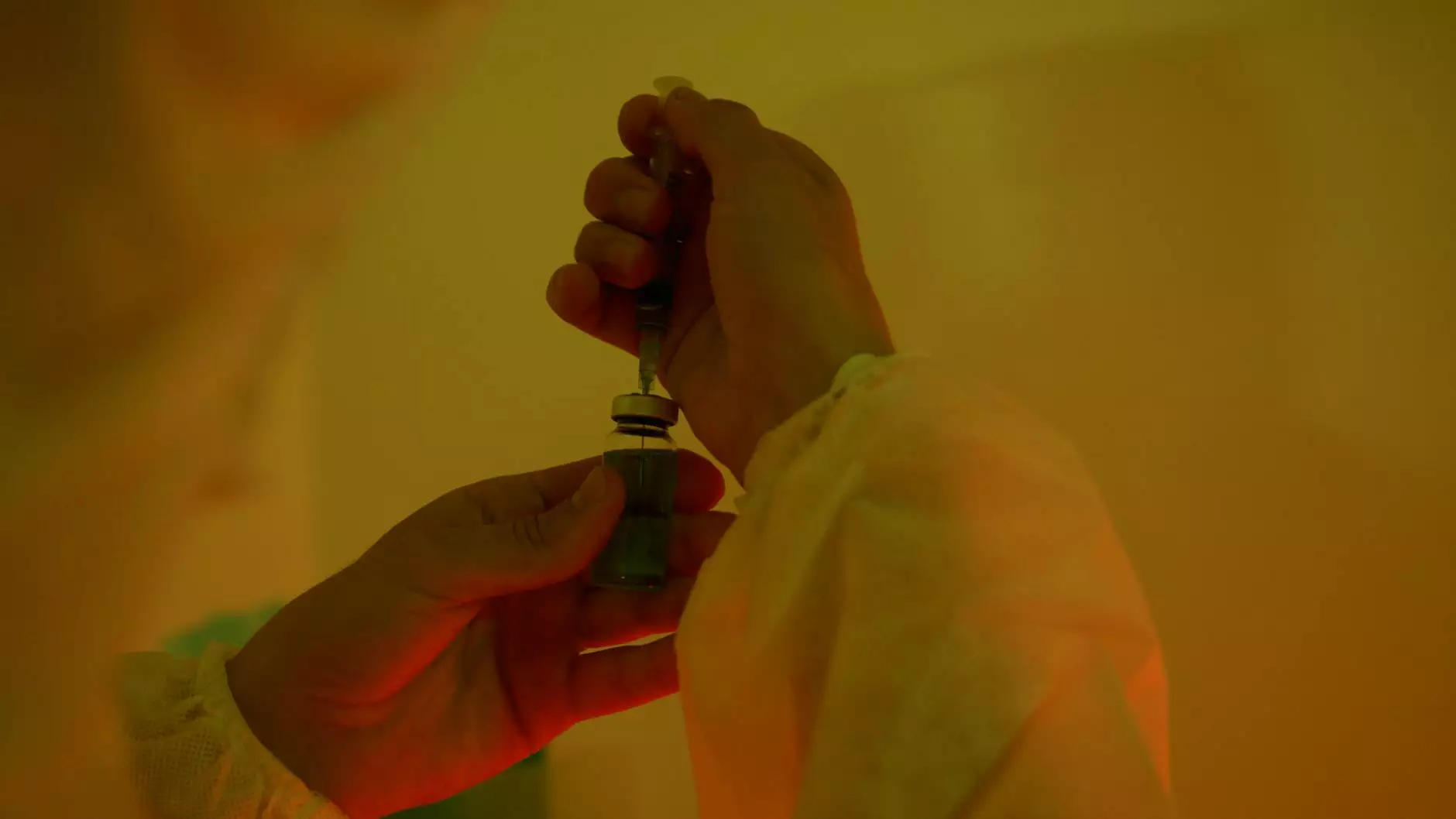
Injection mold manufacturing stands as a testament to modern industrial capabilities, serving as a pivotal process for creating intricate parts across various industries. This method, prevalent among metal fabricators, streamlines the production of complex geometries while maintaining high precision and efficiency.
What is Injection Mold Manufacturing?
At its core, injection mold manufacturing involves injecting molten material into a pre-formed mold to produce a specific part. The materials used can range from plastics and metals to ceramics, but the process remains largely standardized across various applications. This allows manufacturers to produce thousands of identical parts with minimal variation, which is essential in maintaining quality standards.
The Process of Injection Mold Manufacturing
The injection mold manufacturing process can be broken down into several key stages:
- Mold Design: This initial phase involves designing the mold using CAD (Computer-Aided Design) software, allowing for precision and creativity in the design.
- Mold Fabrication: Once the design is finalized, the mold is created using high-quality materials, often through CNC machining, ensuring durability and longevity.
- Material Selection: Different materials are selected based on the desired properties of the final product—be it strength, flexibility, or resistance to temperature variations.
- Injection Process: Molten material is injected into the mold under high pressure, filling the cavity to form intricate parts. This stage requires careful control of temperature and pressure to prevent defects.
- Cooling: The molded parts are cooled within the mold, allowing them to solidify. Cooling time can vary depending on the material and the thickness of the part.
- Part Ejection: After the parts have cooled and solidified, they are ejected from the mold, often requiring trimming or additional processing.
Advantages of Injection Mold Manufacturing
The adoption of injection mold manufacturing offers numerous benefits, particularly for those involved in metal fabrication. Key advantages include:
- High Efficiency: The ability to produce large volumes of parts rapidly reduces overall production time and costs.
- Cost-Effective: While the initial setup costs for molds can be high, the per-part cost decreases significantly with larger production runs, making it economical for mass production.
- Precision and Consistency: The process ensures high dimensional accuracy and repeatability, essential for industries requiring tight tolerances.
- Complex Geometries: Injection molding allows for the production of intricate and complex designs that may be difficult or impossible to achieve with other manufacturing methods.
- Material Versatility: A wide range of materials can be used, including various metals and polymers, allowing for tailored solutions for different applications.
Applications of Injection Mold Manufacturing
Injection mold manufacturing is utilized across various sectors, including:
- Aerospace: Aircraft components often require precision-engineered parts.
- Automotive: From component housings to complex mechatronics, the automotive industry heavily relies on injection molding.
- Consumer Electronics: Small, intricate parts that require precision fit are a staple in electronic assemblies.
- Medical Devices: Injection molding meets the stringent requirements for accuracy and hygiene in medical applications.
- Household Products: Everyday items, from kitchen tools to toys, benefit from the efficiency of this manufacturing process.
The Future of Injection Mold Manufacturing
As technology continues to evolve, so does the injection mold manufacturing industry. Innovations such as additive manufacturing and advanced materials are paving the way for enhanced capabilities. The integration of AI and machine learning for predictive maintenance and quality control is transforming how fabricators approach production.
Industry 4.0 and Smart Manufacturing
The rise of Industry 4.0 is bringing unprecedented changes to manufacturing. Injection mold manufacturing is increasingly incorporating smart technologies, leading to:
- Real-time Monitoring: Sensors embedded in machinery provide data for immediate decision-making, improving efficiency and reducing downtime.
- Predictive Maintenance: Using data analytics, manufacturers can anticipate equipment failures before they occur, saving costs and resources.
- Customization: Advanced technologies enable more customized manufacturing solutions tailored to specific customer needs.
Deepmould.net: A Leader in Metal Fabricators
At deepmould.net, we pride ourselves on being at the forefront of injection mold manufacturing. Our commitment to quality, efficiency, and innovation makes us a preferred partner for businesses looking for reliable solutions in metal fabrication. With state-of-the-art equipment and a team of experienced professionals, we ensure that every project meets the highest standards, from design to delivery.
Our Services
We offer a comprehensive range of services that cater to various manufacturing needs:
- Custom Mold Design: Tailored solutions that meet specific project requirements.
- Rapid Prototyping: Quick turnaround times to help you market your products faster.
- High-Volume Production: Capabilities to scale production up or down based on demand without compromising quality.
- Post-Processing Services: We provide trimming, finishing, and assembly to streamline your supply chain.
Conclusion: The Transformative Power of Injection Mold Manufacturing
In an increasingly competitive marketplace, understanding and leveraging the advantages of injection mold manufacturing is vital for businesses in the metal fabrication industry. With its ability to produce high-quality, complex components efficiently, this manufacturing method is not just a choice—it's an essential investment in the future.
Explore how deepmould.net can help you elevate your production capabilities and achieve unprecedented success in your business ventures. From innovative designs to flawless execution, we are committed to delivering excellence in every project.