Understanding Silicone Injection Molding Machines: Revolutionizing Manufacturing
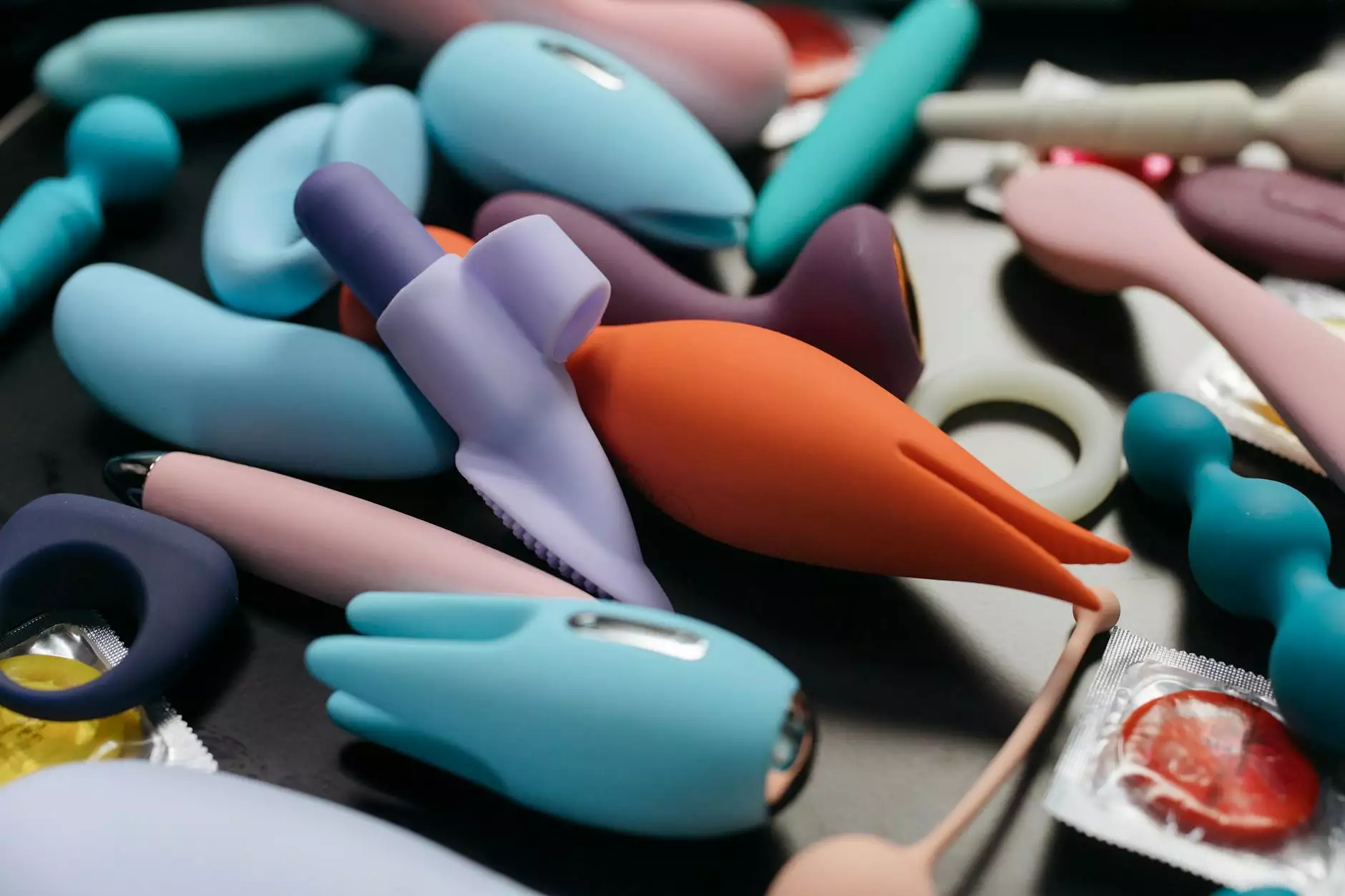
Silicone injection molding machines have become essential tools in modern manufacturing, particularly in industries such as electronics and medical supplies. With their unique ability to produce intricate shapes and reliable products, these machines are pivotal in meeting the high demands of today's consumers. This article delves into the technology behind silicone injection molding, its applications, and its significant impact on various industries.
What is Silicone Injection Molding?
Silicone injection molding is a manufacturing process that involves the creation of silicone rubber products through a precision injection process. This method is known for its efficiency and flexibility, allowing manufacturers to produce complex shapes and components with incredible accuracy.
How Silicone Injection Molding Works
The process begins with silicone material being heated until it reaches a malleable state. Once the silicone is in the correct state, it is injected into a custom-designed mold. After the silicone has cooled and cured, the mold is opened to reveal the finished product. This process allows for:
- High-Volume Production: Silicone injection molding is ideal for mass production, with the ability to produce thousands of identical parts quickly.
- Precision Engineering: The use of molds ensures that every part meets exact specifications, reducing waste and improving quality.
- Flexibility in Design: Manufacturers can create intricate designs that would be difficult or impossible to achieve with other methods.
The Significance of Silicone in Manufacturing
Silicone has become a preferred material in various applications due to its outstanding properties. It is resistant to extreme temperatures, making it suitable for environments where high performance is essential. Additionally, silicone is biocompatible, which is a crucial consideration in the medical and healthcare sectors.
Properties That Make Silicone Ideal for Injection Molding
Several properties contribute to silicone's ideal characteristics for injection molding:
- Durability: Silicone maintains its shape and functionality over time, even under extreme stress.
- Temperature Resistance: It can withstand a broad range of temperatures, making it suitable for various applications.
- Electrical Insulation: Silicone is an excellent insulator, which is particularly beneficial in electronic applications.
Applications in the Electronics Industry
In the electronics industry, silicone injection molding machines are used to create components such as connectors, insulators, and housings that require both durability and precise dimensions. The ability to produce complex geometries aids in designing more efficient and functional electronic devices.
Key Applications in Electronics
- Protective Casings: Silicone molds can create waterproof and dustproof casings for sensitive electronic devices.
- Keypads and Buttons: Custom designs help in manufacturing tactile components that improve user experience.
- Insulation Materials: High-performance insulation components are made to prevent short-circuiting and overheating.
Applications in the Medical Supplies Sector
The medical sector has rapidly adopted silicone injection molding technology due to the stringent requirements for safety and hygiene. Silicone products fabricated through this process are often used for surgical instruments, implants, and various disposable medical devices.
Key Applications in Medical Supplies
- Medical Implants: Silicone's biocompatibility allows for its use in implants that require extensive body integration.
- Surgical Tools: Tools produced with silicone are often lighter and more comfortable for extended use.
- Drug Delivery Systems: Precise molds are necessary for creating reliable and effective drug delivery systems.
Advantages of Using Silicone Injection Molding Machines
There are numerous advantages to using silicone injection molding machines, especially for businesses focused on electronic and medical supplies:
- Cost Efficiency: While the initial setup may be high, the high-volume production capability reduces the cost per part significantly.
- Quality Control: The precision of the molding process allows for rigorous quality control measures, ensuring each part meets standards.
- Environmentally Friendly: Silicone is a sustainable material, and the injection molding process generates minimal waste compared to traditional manufacturing methods.
Challenges in Silicone Injection Molding
Despite many advantages, there are challenges associated with silicone injection molding. These include:
- Initial Investment: The cost of silicone injection molding machines can be substantial, requiring careful financial planning.
- Complexity of Molds: Creating molds for silicone products can be labor-intensive and may require skilled technicians for design.
- Curing Times: Depending on the formulation and thickness, curing times can vary, affecting production schedules.
Nolato: Innovating with Silicone Injection Molding Machines
At Nolato, we pride ourselves on being at the forefront of silicone injection molding technology. Our commitment to quality and innovation ensures that we deliver superior products tailored to the electronics and medical supplies industries. We continually adapt our molding processes to enhance efficiency and meet client needs.
Our Approach to Silicone Injection Molding
We focus on continuous improvement and have invested heavily in state-of-the-art silicone injection molding machines to refine our manufacturing processes. By optimizing machine settings, training our workforce, and utilizing advanced mold designs, we ensure our clients receive products of the highest quality.
Conclusion: The Future of Silicone Injection Molding
As industries continue to evolve, the role of silicone injection molding machines will grow in importance. Manufacturers are increasingly recognizing the benefits of silicone, particularly in sectors where precision and reliability are paramount. The future looks promising, not just for silicone manufacturing but for all the sectors that benefit from it—especially electronics and medical supplies.
Investing in silicone injection molding technology is not merely a trend; it’s a step towards enhanced innovation and higher standards in product quality. Companies like Nolato are leading the charge, setting the stage for exciting advancements in this technology.