Understanding Plastic Injection Molds: A Comprehensive Guide for Metal Fabricators
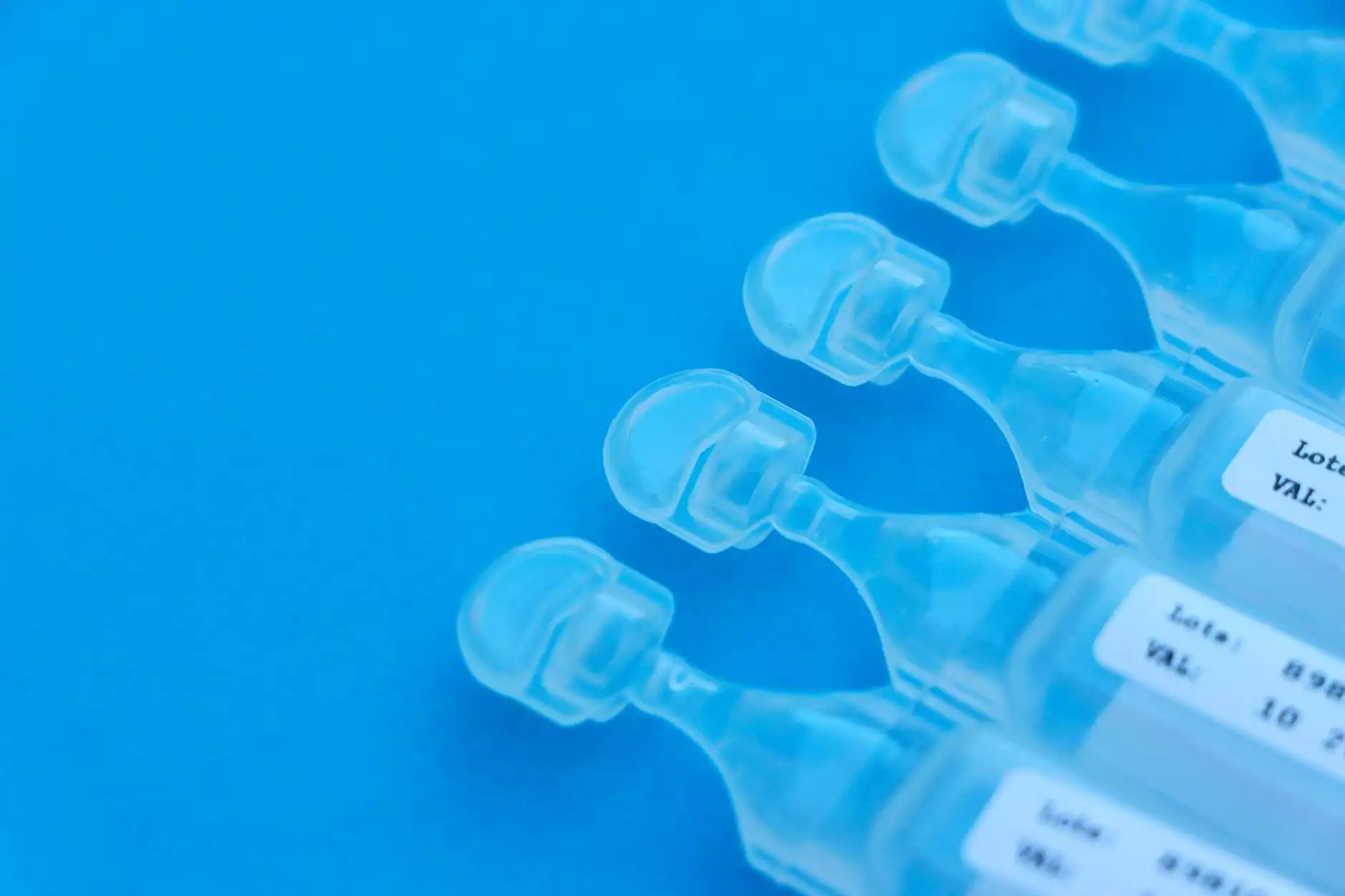
In the realm of manufacturing and metal fabrication, plastic injection molds play a pivotal role. Not only do they allow for the efficient production of complex plastic parts, but they also contribute massively to cost savings, increased production rates, and high-quality finishes. Whether you're a seasoned metal fabricator or just starting in the field, understanding the intricacies of plastic injection molding is essential.
What Are Plastic Injection Molds?
Plastic injection molds are tools used to produce various plastic parts and components through the injection molding process. This method involves injecting molten plastic into a mold cavity where it cools and solidifies into the desired shape. The versatility and efficiency of this process make it a staple in industries ranging from automotive to consumer products.
Key Components of Injection Molding
- Mold Base: The foundational structure supporting the mold.
- Cavities: The hollow spaces in the mold that form the shape of the final product.
- Injection Unit: The mechanism that injects molten plastic into the mold.
- Clamping Unit: Holds the mold together during the injection process.
The Injection Molding Process Explained
The injection molding process involves several crucial steps:
- Preparation of the Mold: The mold must be designed and built to withstand high pressure and temperature.
- Heating of Plastic: Plastic pellets are heated until they melt into a viscous liquid.
- Injection into the Mold: The molten plastic is injected into the mold cavity, taking on its shape.
- Cooling: The material is cooled to solidify before ejection.
- Ejection: The finished part is ejected from the mold, allowing the cycle to repeat.
Advantages of Using Plastic Injection Molds
There are numerous advantages to utilizing plastic injection molds in manufacturing:
- High Efficiency: The process is rapid and can produce large volumes of parts in a short amount of time.
- Complex Geometries: Injection molding allows for the creation of intricate shapes that would be challenging to manufacture with other methods.
- Cost-effective Mass Production: Once the mold is created, producing each part becomes comparatively inexpensive.
- Reduced Waste: The process generates minimal waste material, contributing to more sustainable manufacturing practices.
- Consistent Quality: Each part can be produced with precision, ensuring uniformity and high quality.
Applications of Plastic Injection Molds
Plastic injection molds are utilized across various industries:
Automotive Industry
In the automotive sector, injection molding is essential for creating parts such as dashboard components, exterior trims, and even functional elements like clips and fasteners. The lightweight nature of plastic combined with its ability to withstand environmental challenges makes it an ideal choice.
Consumer Goods
From toys to household items, the consumer goods industry heavily relies on plastic injection molds. The ability to produce durable and attractive designs at speed is invaluable to manufacturers looking to satisfy consumer demand.
Medical Devices
In medical applications, precision is critical. Plastic injection molding enables the production of complex medical devices and components, including syringes, casings, and various surgical tools, while maintaining strict adherence to hygiene standards.
Electronics
As electronics continue to evolve, so does the reliance on injection molding for producing durable casings and internal components. The ability to integrate features like heat resistance and electrical insulation makes plastic injection molds crucial for the electronics industry.
Choosing the Right Plastic Injection Mold Manufacturer
Selecting an appropriate manufacturer for your plastic injection molds is critical for ensuring quality and efficiency. Here are some factors to consider:
- Experience and Expertise: Look for manufacturers with a proven track record in your industry.
- Technology Used: State-of-the-art tech enhances precision, efficiency, and quality.
- Customization Options: Every project is unique; a good manufacturer should offer custom mold solutions.
- Quality Control Measures: Ensure they have stringent QC processes to guarantee the integrity of every mold.
- Customer Support: Responsive and knowledgeable support is essential throughout the manufacturing process.
The Future of Plastic Injection Molding
The future looks bright for plastic injection molds, especially as technology advances. Innovations such as:
- 3D Printing: These technologies are starting to integrate with traditional injection molding, enhancing design flexibilities.
- Biodegradable Plastics: As sustainability becomes paramount, the development of eco-friendly materials for injection molding is advancing.
- Smart Factory Integration: The rise of Industry 4.0 means smarter, more interconnected manufacturing processes.
Sustainability in Plastic Injection Molding
Sustainability is becoming increasingly crucial in manufacturing. The pressure to reduce plastic waste is driving developments towards creating plastic injection molds that support recycling and using eco-friendly materials. Manufacturers are exploring bioplastics and initiatives to recycle used plastic products as part of the injection molding process.
Conclusion
In conclusion, the significance of plastic injection molds in the manufacturing and metal fabrication industries can't be overstated. Their capability to create intricate designs with efficiency, coupled with the ability to mass-produce high-quality items, makes them a critical asset to all sectors. Choosing the right manufacturer like Deep Mould can ensure your production needs are met with precision and care, keeping your business ahead of the competition.
Contact Us
If you're interested in learning more about how plastic injection molds can benefit your manufacturing processes or if you need assistance, don't hesitate to reach out to our experts at Deep Mould. Your journey towards improved productivity and quality starts here.